Maintaining control of environmental conditions is crucial in a compounding pharmacy. All personnel who compound or supervise compounding personnel must undergo initial training and demonstrate competency in compounding sterile preparations and achieving and maintaining appropriate environmental conditions.
USP 797 classifies compounding sterile preparations (CSPs) into three categories based on the level of environmental control during compounding, the likelihood of microbial growth during storage, and the duration within which they must be used.
Category 1: Compounded under the least controlled environmental conditions. These preparations may be prepared in a Primary Engineering Control (PEC) located in an unclassified segregated compounding area. They are assigned a BUD (beyond-use date) of ≤ 12 hours at controlled room temperature or ≤ 24 hours when refrigerated.
Category 2: Require more environmental controls and testing than Category 1. These preparations must be prepared in a cleanroom suite. They may be assigned a BUD of > 12 hours at controlled room temperature or > 24 hours if refrigerated.
Category 3: Undergo sterility testing, supplemented by endotoxin testing when applicable, and have more requirements than Category 2 CSPs for personnel qualification, use of sterile garb, use of sporicidal disinfectants, frequency of environmental monitoring, and stability determination. They have additional requirements that must be met at all times. These preparations may be assigned a BUD longer than established for Category 2 CSPs, up to 180 days.
Before beginning to compound Category 1, 2, or 3 CSPs, personnel are required to successfully complete 3 separate evaluations in succession for hand hygiene, garbing, gloved fingertip and thumb sampling, media fill, and surface sampling.
USP 797 - Personnel Qualification and Environmental Monitoring Requirements (after successful completion of initial competency)
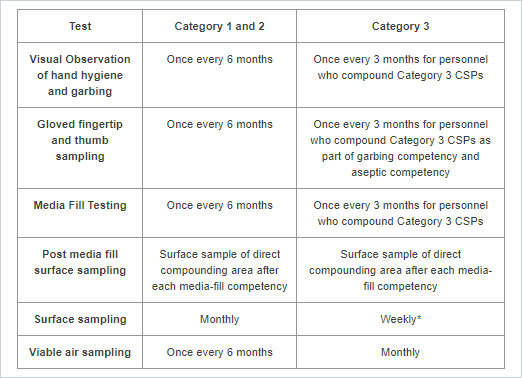
Visual Observation of Hand Hygiene and Garbing: This is a competency evaluation of hand hygiene, garbing procedures, and gloved fingertip and thumb sampling of both hands.
Gloved fingertip and thumb sampling: This test provides data on any microorganisms present on the technician's gloves during compounding. Send plates to ARL for incubation, counting colony forming units (CFUs), and a Certificate of Analysis.
Media Fill Testing: This test assesses the technician's ability to compound aseptically. Send media fill containers to ARL for incubation and observation, and a Certificate of Analysis.
Post-media fill surface sampling test: This test assesses the technician's ability to compound aseptically. At the completion of the media fill qualification process, send surface sample plates to ARL for incubation, counting colony-forming units (CFUs), and a Certificate of Analysis.
Surface sampling: This test monitors surfaces for viable particles. Send plates to ARL for incubation, counting colony-forming units (CFUs), and a Certificate of Analysis.
*For Category 3 CSPs, surface sampling must be completed before assigning a BUD longer than the established limits. Additionally, surface sampling must be conducted within the PEC used to prepare Category 3 CSPs, at the end of each batch before cleaning and disinfection occurs, unless a self-enclosed robotic device is used. When a self-enclosed robotic device is used as the PEC to prepare Category 3 CSPs, surface sampling must be conducted at least once daily at the end of compounding operations, before cleaning and disinfecting occurs.
Viable air sampling: This test monitors air quality for airborne particles. Send plates to ARL for incubation, counting colony-forming units (CFUs), and a Certificate of Analysis.
For more information on personnel qualification and environmental monitoring, contact ARL at info@arlok.com or 800-393-1595.
USP 795 - Personnel Qualifications
All personnel who compound or have direct oversight of compounding nonsterile preparations (CNSPs) must complete training and demonstrate knowledge of principles and competency of skills for performing nonsterile manipulations as applicable to their assigned tasks.
Knowledge and competency must be demonstrated initially and at least every 12 months in at least the following core competencies:
· Hand Hygiene
· Garbing
· Cleaning and Sanitizing
· Handling and transporting components and CNSPs
· Measuring and mixing
· Proper use of equipment and devices selected to compound CNSPs
· Documentation of the compounding process
In addition, a pharmacy’s quality assurance system must ensure that the compounding process consistently meets quality standards, including environmental quality and maintenance.
Resources:
· USP 797 - Pharmaceutical Compounding—Sterile Preparations
· USP 795 - Pharmaceutical Compounding—Nonsterile Preparations
· USP 1116 - Microbiological Control And Monitoring Of Aseptic Processing Environments
· USP 1163 - Quality Assurance In Pharmaceutical Compounding
· FDA Guidance For Industry Sterile Drug Products Produced By Aseptic Processing - Good Manufacturing Practice